Best quality Shell Casting – Gray Iron Sand Casting Company – RMC Foundry Detail:
Gray Iron Sand Casting Company from China with OEM Custom and CNC Machining Services.
Cast iron is an iron-carbon cast alloy with other elements that is made by remelting pig iron, scrap, and other additions. For differentiation from steel and cast steel, cast iron is defined as a cast alloy with a carbon content (min 2.03%) that ensures the solidification of the final phase with a eutectic transformation.
Depending on chemical specifications, cast irons can be non- alloyed or alloyed. The range of alloyed irons is much wider, and they contain either higher amounts of common components, such as silicon and manganese, or special additions, such as nickel, chromium, aluminum, molybdenum, tungsten, copper, vana- dium, titanium, plus others. Generally speaking, the cast iron could be divided into gray iron, ducitle iron (nodular iron), white cast iron, compacted graphite iron and malleable cast iron.
Raw Materials Available for Sand Casting
- • Gray Iron: GJL-100, GJL-150, GJL-200, GJL-250, GJL-300, GJL-350
- • Ductile Iron: GJS-400-18, GJS-40-15, GJS-450-10, GJS-500-7, GJS-600-3, GJS-700-2, GJS-800-2
- • Aluminium and Their Alloys
- • Other Materials and Standards on request
Capabilities of Sand Casting moulded by hand:
- • Max Size: 1,500 mm × 1000 mm × 500 mm
- • Weight Range: 0.5 kg - 500 kg
- • Annual Capacity: 5,000 tons - 6,000 tons
- • Tolerances: On Request.
Capabilities of Sand Casting by Automatic Molding Machines:
- • Max Size: 1,000 mm × 800 mm × 500 mm
- • Weight Range: 0.5 kg - 500 kg
- • Annual Capacity: 8,000 tons - 10,000 tons
- • Tolerances: On Request.
Main Production Procedure
Patterns & Tooling Design → Making Patterns → Moulding Process → Chemical Composition Analysis → Melting & Pouring → Cleaning, Grinding & Shot Blasting → Post Processing or Packing for Shipment
Sand Casting Inspection Capabilities
- • Spectrographic and manual quantitative analysis
- • Metallographic analysis
- • Brinell, Rockwell and Vickers hardness inspection
- • Mechanical property analysis
- • Low and normal temperature impact testing
- • Cleanliness inspection
- • UT, MT and RT inspection
Post-Casting Process
- • Deburring & Cleaning
- • Shot Blasting / Sand Peening
- • Heat Treatment: Normalization, Quench, Tempering, Carburization, Nitriding
- • Surface Treatment: Passivation, Andonizing, Electroplating, Hot Zinc Plating, Zinc Plating, Nickel Plating, Polishing, Electro-Polishing, Painting, GeoMet, Zintec
- • Machining: Turning, Milling, Lathing, Drilling, Honing, Grinding,
General Commerial Terms
- • Main work flow: Inquiry & Quotation → Confirming Details / Cost Reduction Proposals → Tooling Development → Trial Casting → Samples Approval → Trial Order → Mass Production → Continuous Order Proceeding
- • Lead time: Estimatedly 15-25 days for tooling development and estimatedly 20 days for mass production.
- • Payment Terms: To be negotiated.
- • Payment methods: T/T, L/C, West Union, Paypal.
Product detail pictures:
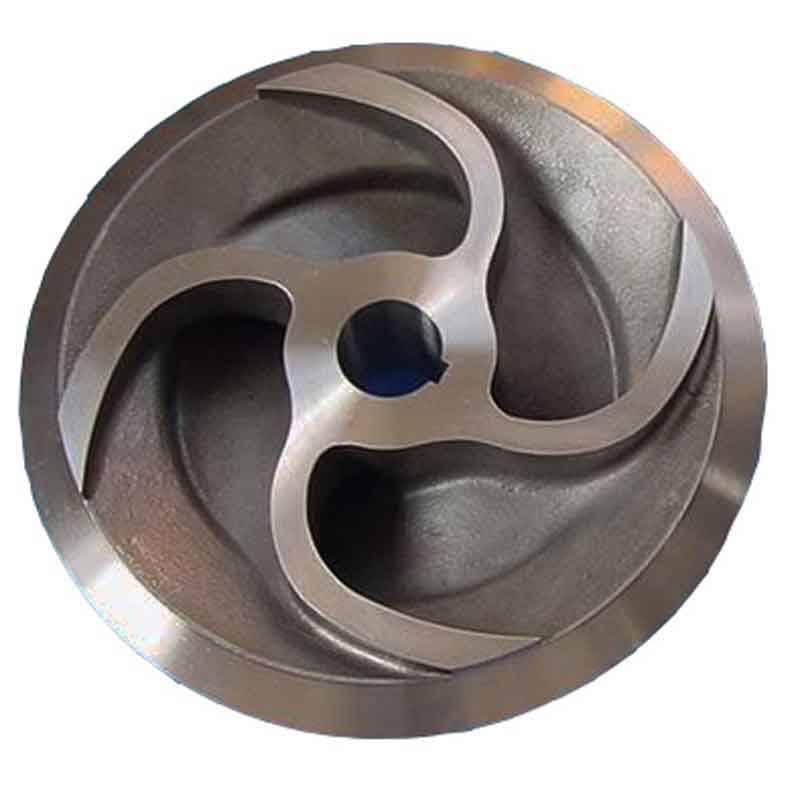


Related Product Guide:
We continue to keep increasing and perfecting our solutions and service. At the same time, we operate actively to do research and enhancement for Best quality Shell Casting – Gray Iron Sand Casting Company – RMC Foundry, The product will supply to all over the world, such as: UAE , Ecuador , Sri Lanka , Whether selecting a current product from our catalog or seeking engineering assistance for your application, you can talk to our customer service center about your sourcing requirements. We can provided good quality with competitive price for you personally.

A nice supplier in this industry, after a detail and careful discussion, we reached a consensus agreement. Hope that we cooperate smoothly.

-
Hot-selling Ductile Iron Casting Products - Su...
-
Discount Price Gray Iron V Process Casting Foun...
-
Professional China Alloy Steel Investment Casti...
-
2020 High quality Vacuum Casting Company - Gra...
-
Cheap PriceList for Carbon Steel Lost Wax Casti...
-
Chinese wholesale Steel Vacuum Casting Supplier...