Good Wholesale Vendors Stainless Steel Sand Casting - Alloy Steel V Process Casting – RMC Foundry Detail:
Cast alloy steel v process castings mean the casting parts produced by vacuum casting process with materials of cast alloy steel.
Vacuum moulding casting, is also called negative pressure molding method, vacuum sealing molding method, or V process for short. This is a relatively new type of physical modeling method. The negative pressure molding method uses the pressure difference between the inside and outside of the mold to fasten the dry and loose sand particles together to obtain a mold with a certain desired shape and a certain strength.
Vacuum casting allows the production of small batches of high quality mouldings in a range of polyurethane resins that replicate the performance of engineering plastics without the high costs of hard tooling associated with injection moulding. The process starts with making a mould by encapsulating a master model in two-part liquid silicone rubber. A vacuum is then applied to remove any trapped air, then it is cured in an oven. Master models can come from a number of 3D printing technologies including stereolithography. Once the silicone is cured, the mould is cut open to form a split line, the master model is removed which leaves a mould cavity perfectly replicating the master model. To make a part, the mould segments are put back together, secured, pre-heated and placed in the vacuum casting system chamber. Two or three part resin is weighed, pigment added if required and the resin parts are placed in the automatic mixer of the vacuum casting system. At this point, the vacuum casting system takes over the process to mix the resin components and vacuum cast the model. Once this is complete the casting is cured. After curing, the mould segments can be separated and the part removed. All that remains is for the casting parts to be trimmed and finished as required.
▶ Vacuum Casting Materials:
• Carbon Steel: Low Carbon Steel, Medium Carbon Steel and High Carbon Steel from AISI 1020 to AISI 1060.
• Cast Steel Alloys: ZG20SiMn, ZG30SiMn, ZG30CrMo, ZG35CrMo, ZG35SiMn, ZG35CrMnSi, ZG40Mn, ZG40Cr, ZG42Cr, ZG42CrMo…etc on request.
• Stainless Steel: AISI 304, AISI 304L, AISI 316, AISI 316L and other stainless steel grade.
• Brass & Copper.
• Other Materials and Standards on request
▶ V Process Casting Capacities:
• Max Size: 1,000 mm × 800 mm × 500 mm
• Weight Range: 0.5 kg – 100 kg
• Annual Capacity: 2,000 tons
• Tolerances: On Request.
▶ Inspecting V-Process Casting Components:
• Spectrographic and manual quantitative analysis
• Metallographic analysis
• Brinell, Rockwell and Vickers hardness inspection
• Mechanical property analysis
• Low and normal temperature impact testing
• Cleanliness inspection
• UT, MT and RT inspection
▶ Vacuum Casting Procedures:
• The pattern is covered tightly by a thin sheet of plastic.
• A flask is placed over the coated pattern and is filled with dry sand without bind.
• The second flak is then placed on top of the sand, and a vacuum draws the sand so that the pattern can be tight and withdrawn. Both halves of the mold are made and assembled in this way.
• During pouring, the mold remains under a vacuum but the casting cavity does not.
• When the metal has solidified, the vacuum is turned off and the sand falls away, releasing the casting.
• Vacuum molding produces casting with high-quality detail and dimensional accuracy.
• It is especially well suited for large, relatively flat castings.
▶ Post-Casting Process
• Deburring & Cleaning
• Shot Blasting / Sand Peening
• Heat Treatment: Normalization, Quench, Tempering, Carburization, Nitriding
• Surface Treatment: Passivation, Andonizing, Electroplating, Hot Zinc Plating, Zinc Plating, Nickel Plating, Polishing, Electro-Polishing, Painting, GeoMet, Zintec.
• Machining: Turning, Milling, Lathing, Drilling, Honing, Grinding.
▶ Why You Choose RMC for V (Vacuum) Process Casting Components?
• Easy recovery of the sand because the binders are not used
• Sand does not require mechanical reconditioning.
• Good air permeability because there is no water is mixed with sand, therefore less casting defects.
• More suitable for large scale castings
• Cost effective, especially for large castings.
Product detail pictures:
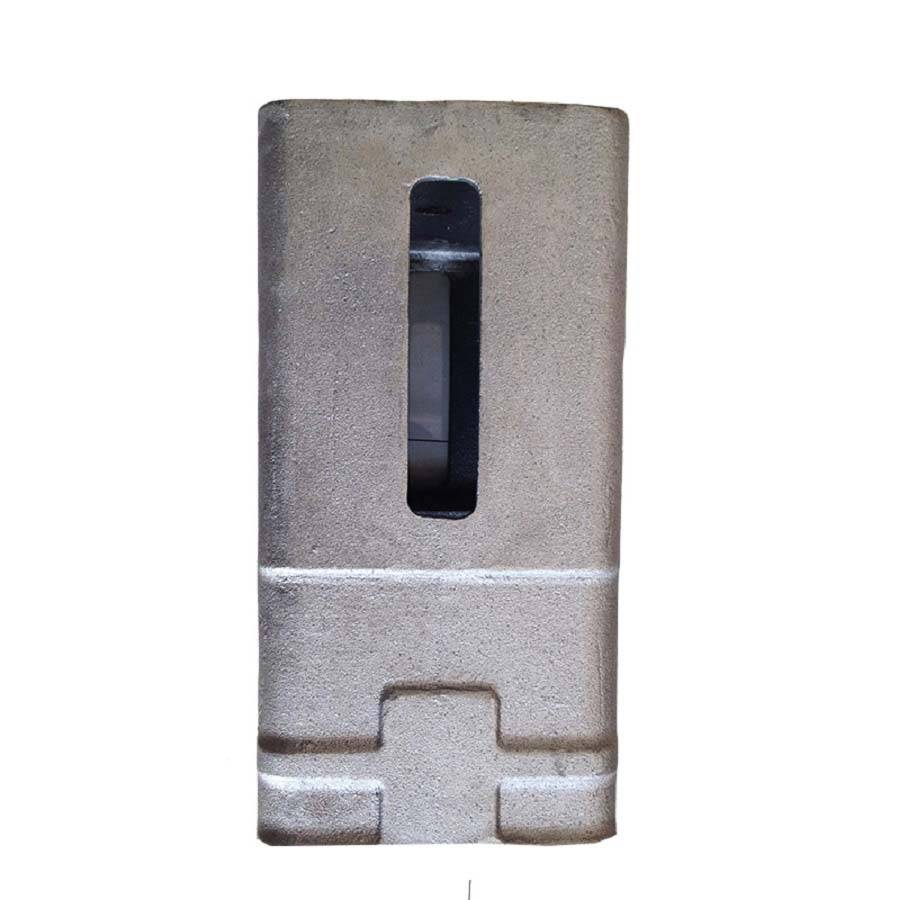
Related Product Guide:
We constantly believe that one's character decides products' high quality, the details decides products' high-quality ,together with the REALISTIC,EFFICIENT AND INNOVATIVE crew spirit for Good Wholesale Vendors Stainless Steel Sand Casting - Alloy Steel V Process Casting – RMC Foundry, The product will supply to all over the world, such as: Thailand , Saudi Arabia , Tunisia , Our organization. Situated inside the national civilized cities, the visitors is very easy, unique geographical and economic situations. We pursue a "people-oriented, meticulous manufacturing, brainstorm, construct brilliant" organization. hilosophy. Strict top quality management, fantastic service, reasonable cost in Myanmar is our stand on the premise of competition. If vital, welcome to make contact with us by our web page or telephone consultation, we've been likely to be pleased to serve you.

We have been appreciated the Chinese manufacturing, this time also did not let us disappoint,good job!

-
Top Suppliers Furan Resin Sand Casting - Custo...
-
Newly Arrival Stainless Steel Precision Casting...
-
Big discounting Alloy Steel Casting Supplier - ...
-
Wholesale Iron Sand Casting Factory - Steel Sa...
-
100% Original Gray Iron Sand Casting Manufactur...
-
China Factory for Aluminium Alloy Precision Cas...