Best quality Ductile Iron Lost Foam Casting Foundry - Alloy Steel Lost Foam Casting Product – RMC Foundry Detail:
Lost Foam Casting refers to the casting method that combines foam patterns with dry sand molding. The molten metal directly fills and replaces the space occupied by the original plastic mold, and directly obtains the required casting after cooling. The foam pattern is directly vaporized during the metal casting process, so the lost foam casting does not require mold removal. At most lost foam casting foundries, the commonly used pattern material is polystyrene.
The Steps of Lost Foam Casting:
1- Use foam molds to produce foam patterns and casting gating systems
2- Bond the patterns and runners to form a mold bundle module
3- Dip paint on the module
4- Dry the paint
5- Put the module into the sand box and fill it with dry sand
6- Vibrate molding in order to fill the cavity with dry sand and then compact the molding sand
7- Pouring molten metal to vaporize the foam and then forming the desired castings
8- After the castings have cooled, clean the castings. The dry sand can be recycled
Advantages of Lost Foam Casting:
1- Lost foam casting is a near-net shape casting method. The dimensional tolerance of the casting can reach CT6~CT9, and the surface roughness is Ra=6.3~50 μm. The shape of lost foam castings can be comparable to resin sand castings.
2- Lost foam casting can produce castings with complex shapes and complex cavities. Compared with the resin sand process, the more sand cores are replaced, the greater the profit margin of lost foam casting. The core competitiveness of lost foam casting is the production of difficult castings with complex inner cavities, such as engine block, engine head and box, etc. These characteristics make the superiority and economic benefits of lost foam casting fully appear, and realize the lightweight and precise casting.
3- Lost foam casting does not require mold removal, which provides greater freedom for casting design and casting process. In terms of process design, the lost foam casting process is first broken into parts and then spliced into a whole, and then the lost foam process is used for integral casting, so that the lost foam casting has the competitive advantage with the traditional sand casting.
4- The use of lost foam casting process can greatly reduce labor intensity, reduce the generation of solid waste, and the used dry sand can be recycled. This feature meets the requirements of energy saving and emission reduction, and has changed the harsh environment of traditional sand casting.
Item | Lost Foam Casting | Vacuum Casting |
Suitable Castings | Small and medium-sized castings with complex cavities, such as engine block, engine cover | Medium and large castings with few or no cavities, such as cast iron counterweights, cast steel axle housings |
Patterns and Plates | Foam patterns made by moldings | Template with suction box |
Sand Box | Bottom or five sides exhaust | Four sides exhaust or with exhaust pipe |
Plastic Film | The top cover is sealed by plastic films | All sides of both halves of sand box are sealed by plastic films |
Coating Materials | Water-based paint with thick coating | Alcohol-based paint with thin coating |
Molding Sand | Coarse dry sand | Fine dry sand |
Vibration Molding | 3 D Vibration | Vertical or Horizontal Vibration |
Pouring | Negative Pouring | Negative Pouring |
Sand Process | Relieve negative pressure, turn over the box to drop sand, and the sand is then reused | Relieve negative pressure, then the dry sand falls into the screen, and the sand is recycled |
Product detail pictures:
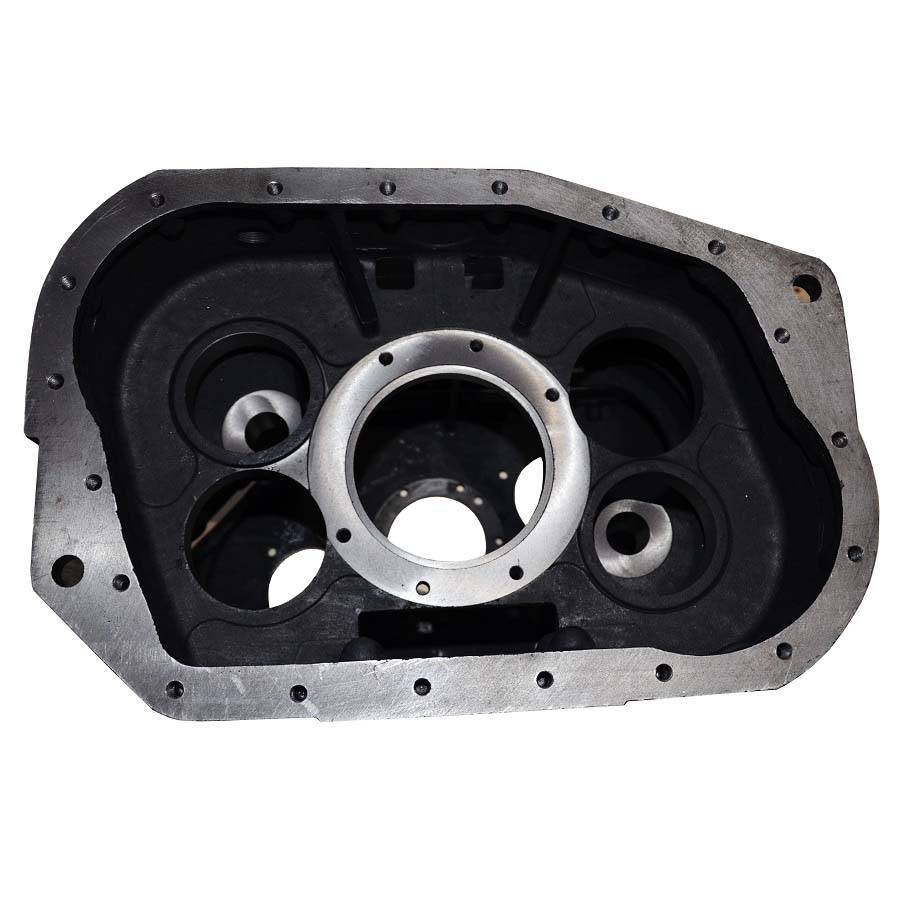
Related Product Guide:
We are going to dedicate ourselves to providing our esteemed buyers together with the most enthusiastically thoughtful products and services for Best quality Ductile Iron Lost Foam Casting Foundry - Alloy Steel Lost Foam Casting Product – RMC Foundry, The product will supply to all over the world, such as: Azerbaijan, Puerto Rico, Malawi, We will initiate the second phase of our development strategy. Our company regards "reasonable prices, efficient production time and good after-sales service" as our tenet. If you are interested in any of our products or would like to discuss a custom order, please feel free to contact us. We are looking forward to forming successful business relationships with new clients around the world in the near future.

The sales manager is very patient, we communicated about three days before we decided to cooperate, finally, we are very satisfied with this cooperation!

-
Super Purchasing for Aluminium Alloy Foundry -...
-
Factory selling Casting Manufacturer - Alloy S...
-
PriceList for No Bake Casting - Custom Brass S...
-
2020 China New Design Duplex Stainless Steel Ca...
-
Cheapest Factory Stainless Steel Casting Manufa...
-
Factory wholesale Steel Lost Foam Casting Found...