2020 High quality Shell Mold Casting Products - Ductile Iron Shell Mold Casting – RMC Foundry Detail:
Ductile Iron Sand Casting Company from China with OEM Custom and CNC Machining Services.
Cast iron is an iron-carbon cast alloy with other elements that is made by remelting pig iron, scrap, and other additions. For differentiation from steel and cast steel, cast iron is defined as a cast alloy with a carbon content (min 2.03%) that ensures the solidification of the final phase with a eutectic transformation.
Depending on chemical specifications, cast irons can be non- alloyed or alloyed. The range of alloyed irons is much wider, and they contain either higher amounts of common components, such as silicon and manganese, or special additions, such as nickel, chromium, aluminum, molybdenum, tungsten, copper, vana- dium, titanium, plus others. Generally speaking, the cast iron could be divided into gray iron, ducitle iron (nodular iron), white cast iron, compacted graphite iron and malleable cast iron.
Shell molding casting process is also called pre-coated resin sand casting process, hot shell molding castings or core casting process. The main molding material is the pre-coated phenolic resin sand, which is more expensive than green sand and furan resin sand. Moreover, this sand can not be recycle used.
The shell molding iron casting parts have higher costs than sand casting. However, the shell molding casting parts have many advantages such as tighter dimensional tolerance, good surface quality and less casting defects.
▶ Shell Molding Casting Raw Materials:
• Cast Carbon Steel: Low Carbon Steel, Medium Carbon Steel and High Carbon Steel from AISI 1020 to AISI 1060.
• Cast Steel Alloys: 20CrMnTi, 20SiMn, 30SiMn, 30CrMo, 35CrMo, 35SiMn, 35CrMnSi, 40Mn, 40Cr, 42Cr, 42CrMo…etc on request.
• Cast Stainless Steel: AISI 304, AISI 304L, AISI 316, AISI 316L and other stainless steel grade.
• Cast Aluminium Alloys.
• Brass & Copper.
• Other Materials and Standards on request
▶ Shell Casting Capacities:
• Max Size: 1,000 mm × 800 mm × 500 mm
• Weight Range: 0.5 kg – 100 kg
• Annual Capacity: 2,000 tons
• Tolerances: On Request.
▶ Inspecting Precision Shell Mold Casting Components:
• Spectrographic and manual quantitative analysis
• Metallographic analysis
• Brinell, Rockwell and Vickers hardness inspection
• Mechanical property analysis
• Low and normal temperature impact testing
• Cleanliness inspection
• UT, MT and RT inspection
▶ Shell Mold Casting Procedures:
✔ Making Metal Patterns. The pre-coated resin sand needs to be heated in the patterns, so metal patterns are the necessary tooling to make shell molding castings.
✔ Making Pre-coated Sand Mold. After installing the metal patterns on the molding machine, the pre-coated resin sand will be shot into the patterns, and after heating, the resin coating will be molten, then the sand molds become solid sand shell and cores.
✔ Melting the Cast Metal. Using induction furnaces, the materials would be melted into liquid, then the chemical compositions of the liquid iron should be analyzed to match the required numbers and percents.
✔ Pouring Metal. When the melted iron meet the requirements, then they will be poured into the shell molds. Based on different characters of the casting design, the shell molds will be buried into green sand or stacked up by layers.
✔ Shot Blasting, Grinding and Cleaning. After the cooling and solidification of the castings, the risers, gates or additional iron should be cut off and removed. Then the iron castings will be cleaned by sand peening equipment or shot blasting machines. After grinding the gating head and parting lines, the finished casting parts would come, waiting for the further processes if needed.
▶ Why You Choose RMC for Shell Mold Casting Components?
✔ Precision and therefore a high material utilization. You will get a net or near-net-shape products after shell molding casting, depending on the requirements of end-users, there will be no or very little machining process is required.
✔ Better surface performance. Thanks to the new-tech materials for molding, the castings from shell molding have a much fine and higher accuracy surface.
✔ A good balanced choice comparing to the sand casting and investment. The shell molding casting have better performance and surface than sand casting, while having much lower costs than precision investment casting.
Product detail pictures:
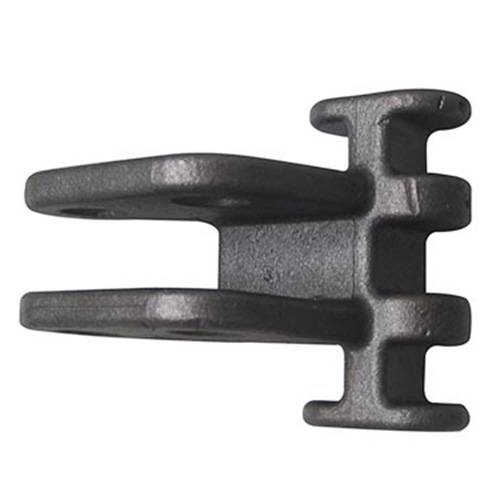
Related Product Guide:
We usually continually offer you the most conscientious consumer services, along with the widest variety of designs and styles with finest materials. These initiatives include the availability of customized designs with speed and dispatch for 2020 High quality Shell Mold Casting Products - Ductile Iron Shell Mold Casting – RMC Foundry, The product will supply to all over the world, such as: Sydney , Riyadh , Luxembourg , Taking the core concept of "to be the Responsible". We will redound up on society for high quality products and good service. We will initiative to participate in international competition to be a first- class manufacturer of this product in the world.

The supplier abide the theory of "quality the basic, trust the first and management the advanced" so that they can ensure a reliable product quality and stable customers.

-
Manufactur standard Gray Iron Green Sand Castin...
-
Lowest Price for Stainless Steel Green Sand Cas...
-
Discount wholesale Metal Foundry - Precipitati...
-
Rapid Delivery for Malleable Casting Factoryiro...
-
Cheapest Price Lost Wax Casting Foundry - Resi...
-
Cheap PriceList for Pre-Coated Sand Casting - ...